Going back to roots, KP Singh sets up automated Jaggery unit, gives higher prices of sugarcane to farmers and employment to villagers
Krishana Pal Singh, a resident of Oon village in Shamli district of Uttar Pradesh, is one such rare personality. After retiring from a key position - Group Head (Technology) of Balrampur chini Mill Group - Singh decided to settle not only in his native village but also develop a nearby village by setting up Hans Heritage Jaggery & Farm Produce. It's an automatic plant for jaggery production which provides employment to more than 50 people of the village. Not only this, farmers are given higher price for sugarcane, which is used as raw material for making jaggery, than the market price.
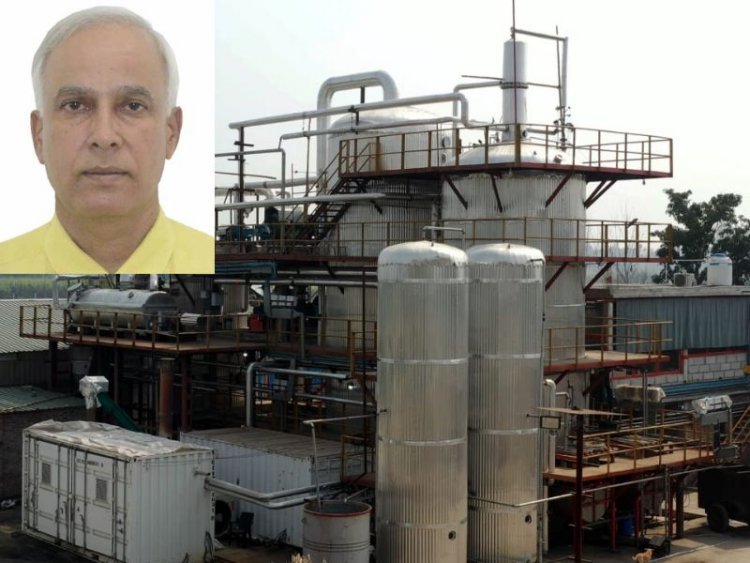
After retiring from job, usually most people who leave their village to earn their livelihood, settle in cities to lead a comfortable life. But there are exceptions. Some people want to return to their village and live in the countryside to fulfill their responsibilities towards their native place. They want to do something so that their place of origin can be developed and employment can be created for the villagers.
Krishana Pal Singh, a resident of Oon village in Shamli district of Uttar Pradesh, is one such rare personality. After retiring from a key position - Group Head (Technology) of Balrampur chini Mill Group - Singh decided to settle not only in his native village but also develop a nearby village by setting up Hans Heritage Jaggery & Farm Produce. It's an automatic plant for jaggery production which provides employment to more than 50 people of the village. Not only this, farmers are given higher price for sugarcane, which is used as raw material for making jaggery, than the market price.
The speciality of his automatic factory is that it not only produces chemical-free jaggery but also does not spread pollution, while the traditional crusher that makes jaggery causes a lot of pollution. Apart from this, jaggery processing is also very easy in this factory. After inserting sugarcane from one end, jaggery gets ready and comes out in different shapes from the other end.
Talking about his post-retirement journey, Singh told the Rural Voice, “I had decided to settle in my village five years before retirement and thought that I would do something different by coming to my village. It is not possible to live only by farming in today's world. But since 5-7 years back I had something in my mind about how to do something for the farmers, I used to think if I could give something back to the village, the society, the area from which I have moved ahead, it would be my good fortune.
"That's why I started working on it even before retirement. Since I have been closely associated with the sugar and jaggery industry, it was easier for me to work in this sector than in other sectors. Also I am from sugarcane belt. Apart from this, I also have cultivable land."
Krishana Pal Singh says, “Today the quality of jaggery has deteriorated. No one makes jaggery without chemicals. Jaggery with chemicals damages liver, kidney, bones. Chemicals are mixed in jaggery, sugar is also mixed. Our jaggery is rich in calcium, magnesium, potassium, iron, vitamins and proteins. It contains 80-85 per cent sugar and 15-20 per cent nutrients. Jaggery from Kolhu crusher contains 90-95 per cent sugar.
“Besides, the Shamli sugar mill pays sugarcane to the farmers after one year. Kolhu crusher millers also do not leave any chance to loot the farmers. There was also that angle. That's why I have decided to give sugarcane price to the farmers a minimum of Rs 25 per quintal more than others, there is no limit on the maximum. I have also promised the farmers that if I get more profit, I will share that profit with the farmers.
"Production started in my factory in December 2022 and at that time farmers were getting Rs 225-250 per quintal in the market. I started buying at Rs 275 which later went up to Rs 340-350 per quintal. My dream seems to be coming true now."
Krishana Pal Singh has been concerned about pollution since the beginning. He says that by burning leaves or paddy straw in the field, the farmers are doing their own loss. Because of this there is no carbon left in the ground. First the sulfur ran out, then the zinc ran out. When sulfur and zinc started getting mixed in the form of chemicals, farmers started putting it in sugarcane. Carbon is available from leaves, cow dung and organic manure. If this is not compensated, then a big problem will arise for agriculture, because carbon is not available in the form of chemical at present, which we can put in the fields. They say that the process of burning leaves and stubble has broken the natural cycle.
"That's why it was in my mind that such a factory should be set up so that pollution does not spread at all. It is a completely pollution-free factory. Even while being associated with the Balrampur Sugar Group, I installed 4-5 sugar mills which are fully modern and automatic and spread less pollution. I have used the same technology but my factory does not have boiler and furnace that is the difference."
The capacity of this factory is to crush 2,500 quintals of sugarcane per day. Its speciality is that it has three per cent more recovery as compared to crusher. The recovery in Kolhu crusher is 12 per cent and in Singh’s automated plant it is 15 per cent. Due to this also, K P Singh is able to give higher price of sugarcane to the farmers.
"Due to higher recovery from modern technology, we will soon become profitable. At present, my jaggery has been well received in Gujarat and is being supplied in the market there. Demand has also emerged from some markets of Haryana. This is the first year and this year the production of jaggery was about 13,000 quintals. As the market grows, production will increase."
The cost of this factory has come to around Rs 12 crore. For this, he has neither taken any help from the government nor has taken loan from the banks. Apart from his own money, he has managed to set it up with the help of some close friends. He told the Rural Voice that his next project is to make bio-CNG from sugarcane bagasse.